One-Stop Shop: NVision's Comprehensive Reverse Engineering and Expanded Metallurgy Services Draws Rave Reviews
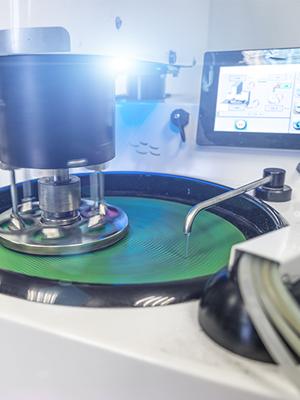
When a leading aerospace company faced the challenge of replicating critical components without original design documentation, it turned to NVision, Inc. (Southlake, TX). NVision provides complete reverse engineering, encompassing 3D scanning, CAD modeling, 2D drawings, and materials analysis. Leveraging its advanced scanning/measurement, engineering, and metallurgy capabilities, NVision delivered a complete solution that ensured top-to-bottom replication accuracy.
“Their thorough, comprehensive reverse engineering not only met but exceeded our expectations,” said the aerospace firm’s Quality Control Manager. “As a result, we experienced accelerated design turnaround and a significant reduction in manufacturing risks and associated costs. The best part was we didn’t have to work with multiple companies–NVision is a one-stop shop. They handled every aspect of the process and knew the right questions to ask.”
The Aerospace Facility
For over 40 years, the FAA-certified aircraft facility has served the aviation industry with precision and reliability. Specializing in aircraft components and assemblies, the company’s operations include Non-Destructive Testing (NDT), in-house machine shop services, parts sales and sourcing, and more. Over the decades, the company has earned a global reputation for quality workmanship and outstanding customer service, becoming a trusted partner to aviation professionals worldwide.
A recent project posed a challenge that would have been nearly impossible to solve in the past: to complete a complex assembly overhaul, the company needed precise digital reproductions of two key components—a piston and an integrated sleeve—without access to original CAD files or material specifications.
Why and How Comprehensive Reverse Engineering Matters
Many aerospace specialists must work with legacy parts that lack up-to-date documentation. Without high-precision reverse engineering, replicating these parts can result in:
- Improper fit
- Suboptimal materials
- Reduced product life
- Rework and costly delays
NVision’s comprehensive reverse engineering eliminates these risks by combining dimensional accuracy, CAD expertise, and detailed materials analysis to ensure precision and performance.
Pistons and Other Essential Components
Pistons, integrated sleeves, and other parts are critical components in aerospace systems. The piston in this case is small, cylindrical, and transfers hydraulic force to an aircraft’s rotating components. The other part, a small ring-shaped integrated sleeve, regulates energy transfer and wear. Both components require extremely tight tolerances and must be made from materials capable of withstanding extreme pressure, heat, and wear.
To ensure functionally identical replacements, NVision fully characterized each part, both dimensionally and metallurgically, prior to modeling.
The Reverse Engineering Challenge
The aerospace facility needed three things: precise part dimensions, confirmed material composition, and production-ready blueprints. Without original documentation, the risk of delays, performance issues, and expensive rework loomed large.
NVision stepped in with its full-service reverse engineering solution. Combining cutting-edge technology with decades of experience, NVision’s ultra-high-precision 3D scanners (laser, structured light, and more) captured millions of data points in minutes—ideal for delicate, complex parts.
After scanning, the data was converted into detailed surface models and then into solid CAD files for:
- Reverse engineering
- CNC machining
- Quality inspection
- Stress simulations
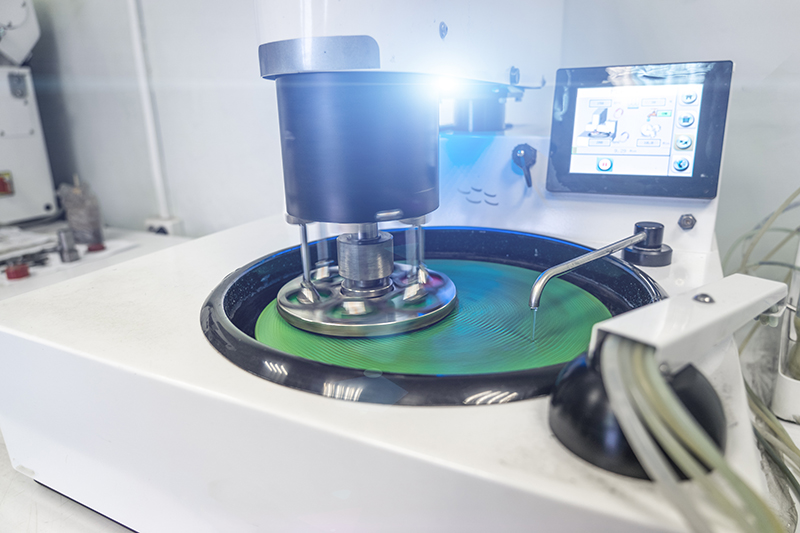
NVision’s metallurgical testing identifies alloy composition, heat treatments, and potential structural issues to ensure that replacement parts meet or exceed the original performance standards.
Inside NVision’s Complete Reverse Engineering Process
1. 3D Scanning
Parts Involved:
- Piston (approximately 2 inches in length and 1 inch in diameter)
- Integrated sleeve (roughly 0.3 inches in outer diameter, 0.12 inches inner diameter, and 0.3 inches tall)
NVision examined five parts in total: two were designated for materials analysis and three for 3D scanning. Using ultra-high-precision laser systems, they captured the part's geometry down to microns. Key considerations included:
- Multiple Sample Scans: To account for minor dimensional variations, NVision scanned multiple sleeves and averaged the data to ensure consistent and accurate modeling.
- Internal Geometry Capture: The piston required detailed internal scanning, a challenging process due to its compact, cylindrical structure.
2. CAD Model Creation
After scanning, NVision created high-resolution 3D CAD models. The client received models in multiple formats, including SolidWorks native files and IGES/STEP files.
NVision also provided optional 2D technical drawings to support machine shop manufacturing.
3. Materials Testing and Metallurgical Analysis
Since form alone doesn’t guarantee function, a critical element of NVision’s reverse engineering process is comprehensive materials testing.
“To fully duplicate a part’s performance, you need more than just its measurements; you also need to know its material composition, “ explains Steve Kersen, NVision’s president. “For example, you may have the complete dimensional details of a jackhammer, but if you build it with plastic instead of steel, it will be the jackhammer that breaks, not the concrete.
“We want to determine what type of metal the part is made from, what kinds of treatments—such as heat treatment—it has undergone, the composition of its surface finish, and its tensile strength. We conduct a wide range of analyses, including metallographic examination, hardness and impact testing, and identify and map corrosion, decarburization, and other structural conditions.”
Using advanced instrumentation, NVision performed both quantitative chemical and physical analyses to identify each part’s precise alloy composition, surface coatings, and any post-manufacturing treatments such as plating or heat treating.
For example, chemical analysis confirmed the piston to be a heat-treated stainless steel alloy closely matching Martensitic Chromium Stainless Steel,with a corrosion-resistant surface finish. It uncoated surface had been bead-blasted using silicon carbide and alumina to enhance durability and surface integrity. The part contains elevated levels of carbon, nickel, and copper, which contribute to improved strength, hardness, and wear resistance—ideal for high-stress, high-wear applications.
The integrated sleeve was determined to be made from a material consistent with Free-Cutting Brass, a copper alloy prized for its excellent machinability, wear resistance, and structural stability. The sleeve’s outer surface was revealed to be coated with silicone oil, and no plated metals were detected using energy-dispersive (ED) spectrometry.
By fully characterizing the material composition and treatment history of both parts, NVision enabled the fabrication of replacements that not only matched the original components in shape and size but also met, or even exceeded, their mechanical and thermal performance in real-world operating conditions.
Fast, Accurate Delivery
From part receipt to data delivery, the entire project was completed in just ten business days.
“I was very impressed with NVision’s quick turnaround time and the high level of detail they provided,” said the Quality Control Manager. "NVision even ran extra scans to calculate better averages. The result was far more accurate than anything we could’ve assembled in-house.”
Conclusion: A Successful Partnership
NVision’s comprehensive reverse engineering service, integrating high-resolution scanning, CAD modeling, and materials analysis/metallurgical testing, delivered value in four key areas:
- Speed: Project completed in under two weeks
- Precision: Sub-millimeter accuracy in scanning and modeling
- Material Insight: Metallurgical confirmation of all materials
- Manufacturing Readiness: CAD files and prints ready for fabrication
“NVision's solution was complete, precise, and timely,” said the Quality Control Manager. “It gave us everything we needed to replicate the parts with confidence. Their one-stop solution reduces vendor complexity, improves technical accuracy, speeds time to market–and provides peace of mind!”.
More and more manufacturers and facilities are discovering the advantages of NVision’s comprehensive approach to reverse engineering. By combining 3D scanning, CAD modeling, materials analysis, and metallurgical testing—all under one roof—NVision delivers results that are faster, more accurate, and more complete than traditional methods, benefiting a broad range of industries.
Please contact us by phone (817.416.8006) or email (sales@nvision3d.com) or send us a detailed message through our contact form